One of the key insights I’ve gathered with Lean over the years is learning to keep on improving. The improving part is usually the easiest : find a problem and solve it. I can ask any developer in my company and given the time slot, he’ll do something.

Reading The Toyota Way of Dantotsu Radical Quality Improvement by Sadao Nomura, I was particularly impressed by the keep on part since it’s the difficult chunk.
The first example is the sensei’s timetable. The schedule is done yearly : it’s not some improvised visit but a recurrent trip (3 times a year) over a long period (9 years in total). And there’s no shortage of repetition.
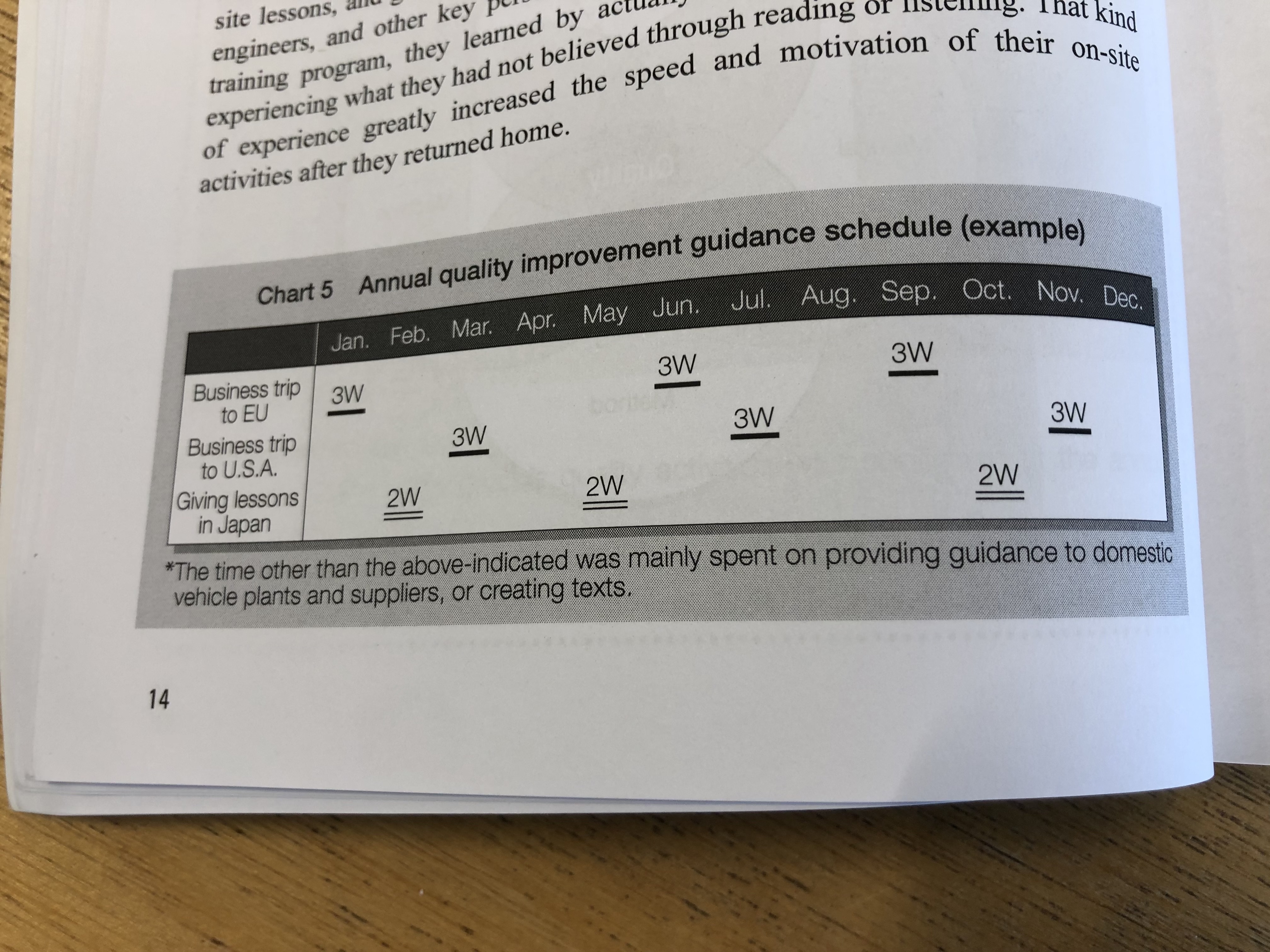
For overseas employees, the Toyota Production System (TPS) seemed to have some unbelievable points, no matter how much they read the relevant books or learned from others. Therefore, I decided to hold a 2-week TPS training program in Japan three or four times a year in addition to the local on-site lessons, and gave the experience to 100 or more managers, team leaders, engineers, and other key persons coming from each company. Through this training program, they learned by actually seeing with their own eyes and experiencing what they had not believed through reading or listening.
Another example is the number of successive countermeasures taken against problems found on the Gemba.
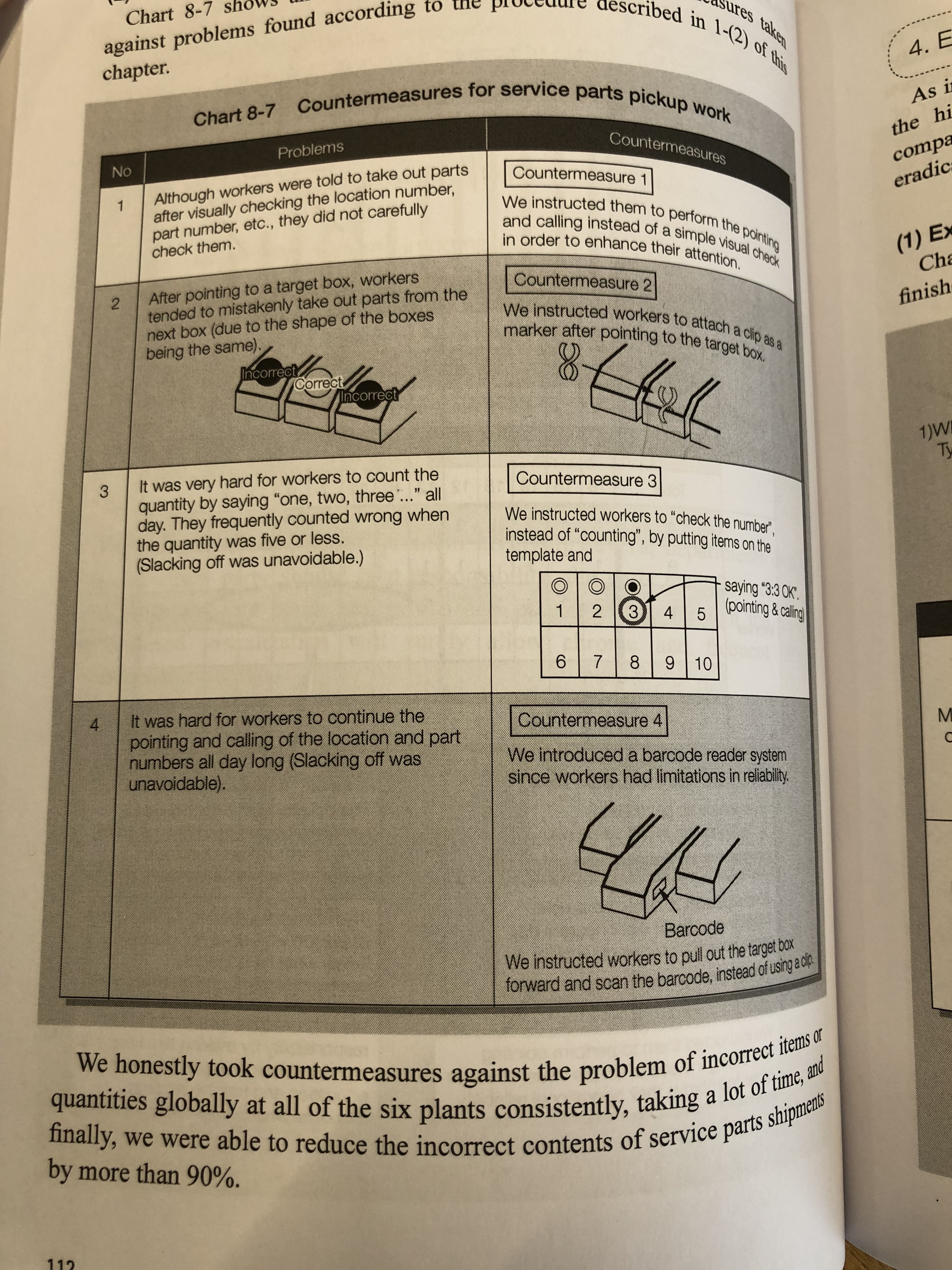
There’s no magic silver bullet : it’s always about digging deeper until a root cause is found. Rinse and repeat as some would suggest.