Even though Toyota created Lean (or TPS as it’s called inside of the car company) within its manufacturing plants, this « business strategy » has had tremendous success in all different types of companies : consumer electronics (Apple - with Steve Jobs as its Chief Engineer), fashion (Zara - with its focus on putting consumers in charge) or e-commerce (Amazon - using andon cords, Kaizen programs, and eliminating the root cause of errors).
Recently Toyota has seen a new surge in TPS training for its office staff. And its suppliers are taking notice : « Toyota, are you committed? » said one.
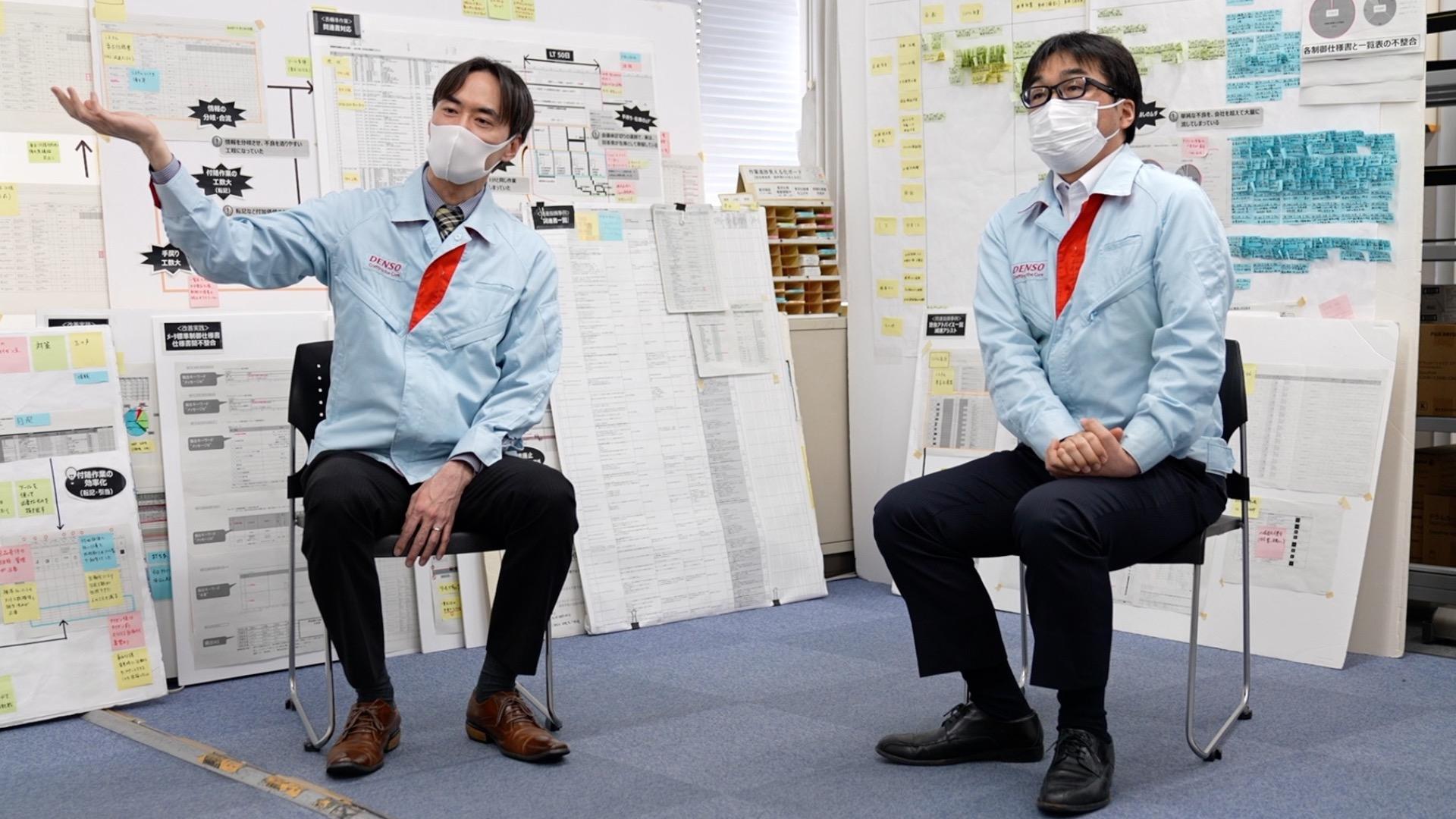
We were told about it in September last year, and the first thing I said was, “Are you committed?” because I wanted to know from the start how deeply we were to get involved in it. I wanted to know this, because we had worked on the same initiative with Toyota in the past on several other occasions. (…) This isn’t easy to say, but in the past, I feel that Toyota has given up in the middle of some projects. Based on such past experience, I wanted to know from them how committed they are this time and how they plan to make changes.
What a lesson in Respect for People when you accept to transcribe such powerful statement on your own website. Because challenging misconceptions is always hard, implementing Lean is never easy and it starts with facing the reality as it is.