When I am asked to describe what changed when we added kanbans to our work practices, I usually start explaining the difference between driving the pace in the office with a due date (« this piece of work should be done by Friday afternoon ») or a start date (« you should start working on this piece of work on Tuesday »).
In the first context, the not-so-subtle advice is you can work overtime and/or over the week-end to finish it off. The manager will only see it on his desk on the following Monday early morning anyway. Unleashing the compliance spirit if necessary, trying to find to whom the blame can be attributed.
In the second context, an andon will be triggered as soon as Tuesday if work isn’t started. The chain of help will be activated and the manager should be at hand, trying to understand the problem, its sources and its consequences. And then trying to get everything back in shape before the customer is impacted : he has until the Friday afternoon to mitigate the problem.
The role of the manager changes completely. The « power over » is gone. In the words of Masaaki Imai in his Strategic Kaizen, he becomes an entropy fighter:
Shop floors are fraught with abnormalities that disrupt smooth flow. Every time it happens, it is management’s task to bring it back to normalcy. Even when no problem seems to exist and everything seems to be under control, one should be reminded that anything and everything that goes on the shop floor is destined to deteriorate on its own if left alone.
And since no Lean concept would be entirely adequate without its Japanese word, Masaaki Imai introduces baratsuki (ばらつき), ie. scattering or dispersion. In the Nassim Nicholas Taleb’s tradition of Via Negativa, it becomes taming the baratsuki.
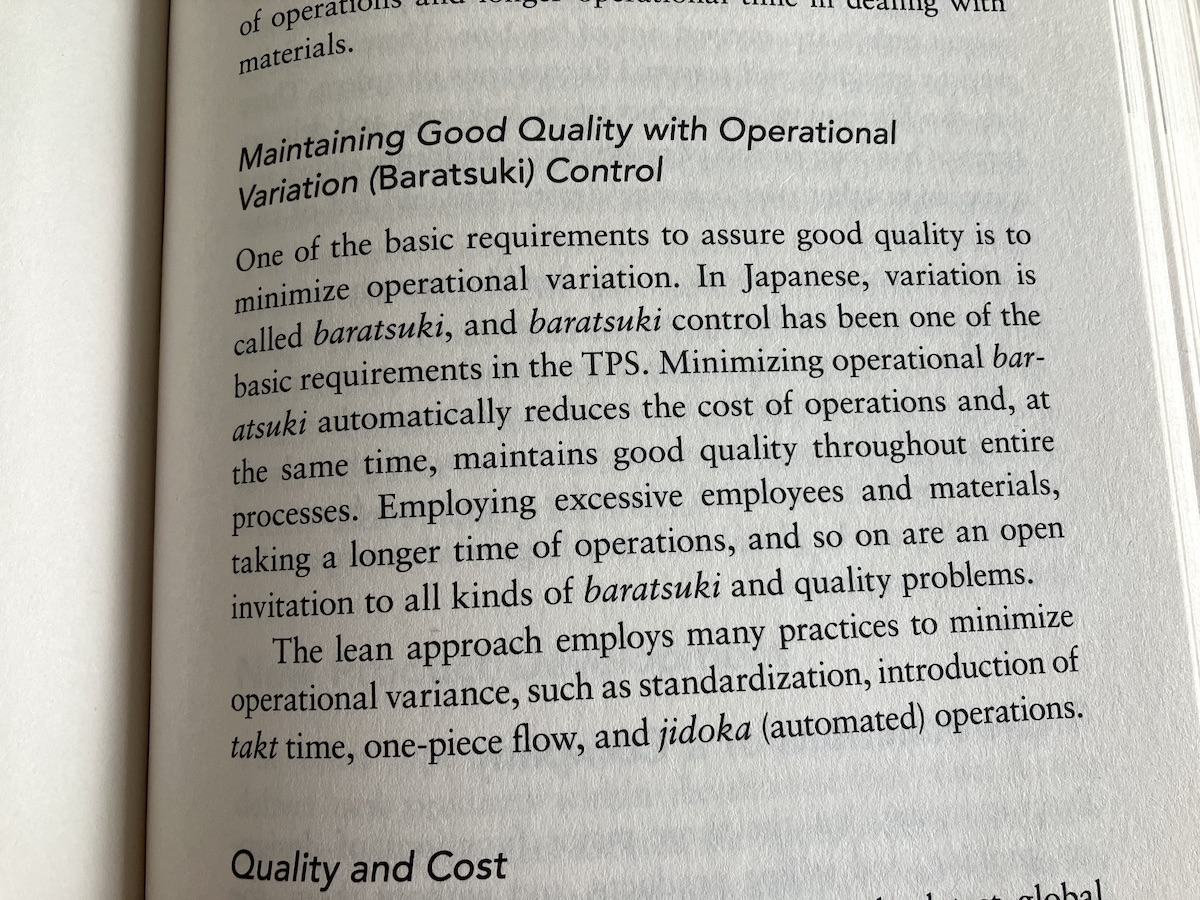
The Lean tools become a mean to ensure the entire team can produce good quality work. And kanbans are no exceptions.